Was ist Sandguss und was sind seine Vorteile?
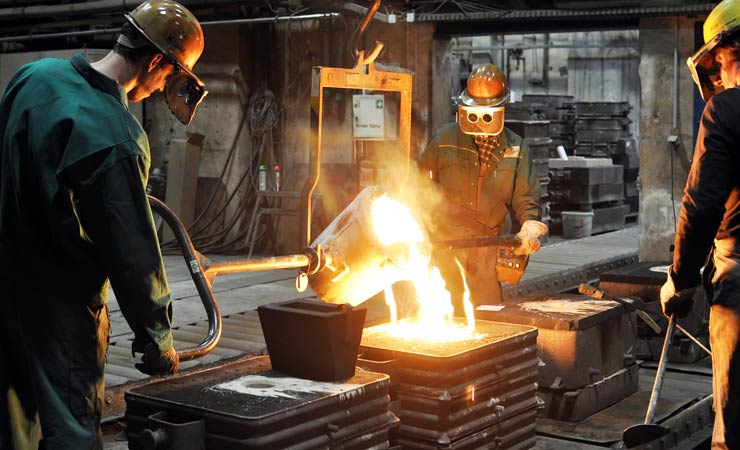
Der Sandguss ist ein bewährtes Verfahren zur Herstellung von Werkstücken aus Metall, bei dem eine Form aus speziellem Sandmaterial als Negativvorlage dient. Es gehört zu den ältesten und am weitesten verbreiteten Gießverfahren und zeichnet sich durch seine Flexibilität und Anpassungsfähigkeit aus. Das Grundprinzip des Sandgussverfahrens basiert auf der Verwendung einer einteiligen oder mehrteiligen Form, die aus verdichtetem Formsand besteht. Dieser Sand wird um ein Modell herum verdichtet, das die spätere Geometrie des Gussstücks vorgibt. Nach der Entfernung des Modells entsteht eine Formhöhlung, in die flüssiges Metall gegossen wird. Nach der Erstarrung des Metalls wird die Sandform zerstört, um das fertige Bauteil zu entnehmen.
Die Zusammensetzung des verwendeten Formsandes spielt eine zentrale Rolle für die Qualität des Endprodukts. Der Sand wird mit Bindemitteln und Additiven versehen, um die notwendige Stabilität und Hitzebeständigkeit während des Gießprozesses zu gewährleisten. Das Verfahren eignet sich besonders für die Herstellung von Bauteilen mit komplexen Geometrien und ermöglicht eine hohe Präzision in der Formgebung.
Durch die Möglichkeit, Formen individuell und kosteneffizient anzupassen, hat sich der Sandguss in zahlreichen Industriezweigen etabliert. Neben der Herstellung einfacher Bauteile können auch hochkomplexe Strukturen realisiert werden, die in anderen Verfahren nur schwer oder gar nicht umsetzbar wären.
Technologische Grundlagen des Sandgussverfahrens
Der Aufbau der Sandform ist ein zentraler Aspekt des Sandgussverfahren und bestimmt maßgeblich die Qualität und Präzision des fertigen Gussstücks. Eine typische Sandform besteht aus einem Formrahmen, dem sogenannten Kasten, in den der Formsand eingebracht und verdichtet wird. Dabei wird eine exakte Abbildung des gewünschten Bauteils erstellt. Für besonders komplexe Strukturen kommen zusätzlich Sandkerne zum Einsatz, die Hohlräume oder spezielle Konturen im Gussstück ermöglichen.
Die Zusammensetzung des Formsandes variiert je nach den Anforderungen des Gießprozesses. Häufig verwendete Sande sind Quarzsand, Chromitsand und Zirkonsand, die durch ihre thermische Stabilität und ihre Kornstruktur überzeugen. Diese Sande werden mit Bindemitteln wie Ton, Kunstharzen oder anorganischen Verbindungen kombiniert, um die Festigkeit und Formstabilität während des Gießens sicherzustellen. Zusätzlich können Additive wie Kohlenstoff oder spezielle Pulver hinzugefügt werden, um die Oberflächenqualität des Gussstücks zu verbessern.
Neben der Sandform selbst ist eine Reihe von Werkzeugen und Ausrüstungen erforderlich, um den Gießprozess effizient und präzise durchzuführen.
Dazu gehören Formrahmen, Modellplatten und Kernkästen, die zur Herstellung der Form und der Kerne verwendet werden. Außerdem kommen Maschinen zur Verdichtung des Sands, sogenannte Formmaschinen, sowie Öfen für das Schmelzen des Metalls und Gießhilfen wie Schöpfkellen und Tiegel zum Einsatz. Für die Nachbearbeitung der Gussstücke werden Werkzeuge zur Entgratung und Reinigung benötigt.
Die Kombination aus hochwertigem Formsand, geeigneten Bindemitteln und einer effizienten Ausrüstung bildet die Grundlage eines erfolgreichen Sandgussverfahrens. Diese technologischen Grundlagen ermöglichen die Produktion komplexer und zuverlässiger Bauteile und tragen zur Vielseitigkeit des Verfahrens bei.
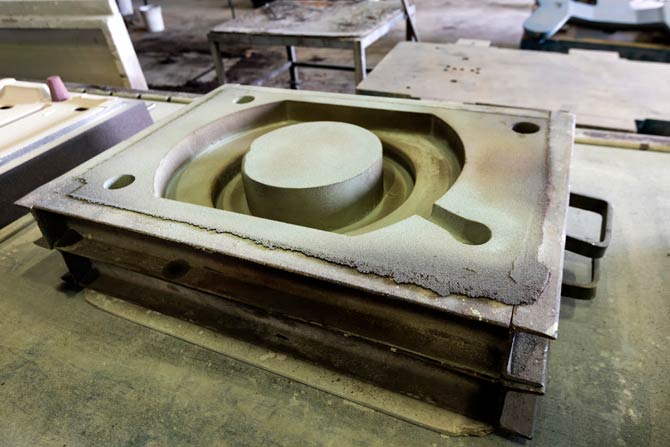
Prozessablauf beim Sandguss
Der Sandgussprozess beginnt mit der Herstellung der Modellform, die als Vorlage für das spätere Gussstück dient. Das Modell, häufig aus Holz, Kunststoff oder Metall gefertigt, wird in eine Formkiste eingebracht und mit Formsand umgeben. Durch Verdichtung des Sandes entsteht eine stabile Form, die die Konturen des Modells exakt abbildet. Für Bauteile mit inneren Hohlräumen werden Kerne gefertigt, die ebenfalls aus speziellem Formsand bestehen und passgenau in die Form eingesetzt werden.
Nach der Fertigstellung der Sandform und der Platzierung der Kerne erfolgt das Gießen. Das Metall wird in einem Ofen auf die gewünschte Temperatur erhitzt und anschließend in die Formhöhlung gegossen. Der Gießvorgang erfordert Präzision, um eine gleichmäßige Füllung der Form zu gewährleisten und Materialfehler wie Lunker oder Lufteinschlüsse zu vermeiden. Nach dem Gießen erstarrt das Metall in der Form, wobei sich die Struktur des Bauteils durch die kontrollierte Abkühlung festigt.
Nach der Erstarrung wird das Gussstück durch Entformung aus der Sandform gelöst. Dieser Schritt erfolgt durch mechanisches Zerlegen der Form, da diese in der Regel nur einmal verwendet werden kann. Anschließend wird das Bauteil von anhaftendem Formsand gereinigt, und überschüssige Metallteile wie Angüsse oder Speiser werden entfernt. Die Nachbearbeitung kann weitere Arbeitsschritte umfassen, etwa Schleifen, Polieren oder Bohren, um die Oberflächenqualität zu verbessern und das Bauteil auf die endgültigen Maße zu bringen.
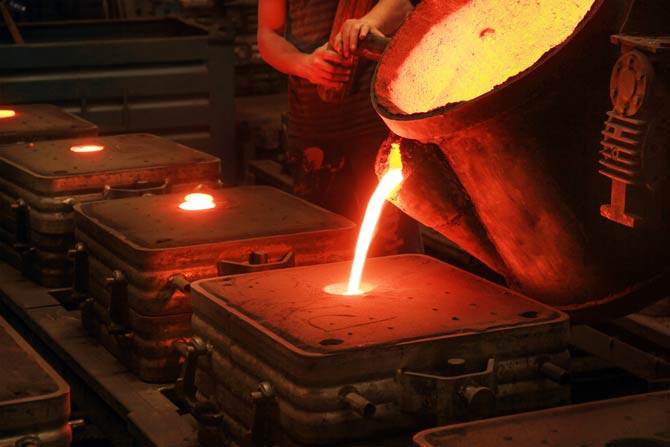
Vorteile des Sandgussverfahrens
Das Sandgussverfahren bietet eine außergewöhnliche Flexibilität, insbesondere bei der Herstellung von Bauteilen mit komplexen Geometrien. Die Formbarkeit des verwendeten Materials ermöglicht es, selbst anspruchsvolle Designs und feinste Details präzise abzubilden. Dadurch können Gussstücke realisiert werden, die mit anderen Verfahren oft nur schwer oder gar nicht umsetzbar sind.
Ein weiterer wesentlicher Vorteil des Sandgussverfahrens liegt in seiner Wirtschaftlichkeit, besonders bei Kleinserien und Prototypen.
Die geringe Abhängigkeit von kostenintensiven Dauerformen reduziert die anfänglichen Investitionen erheblich, was die Fertigung kleiner Stückzahlen kosteneffizient macht. Gleichzeitig erlaubt das Verfahren eine schnelle Anpassung an geänderte Konstruktionsvorgaben, was es besonders für Entwicklungsprojekte attraktiv macht.
Die breite Materialvielfalt, die im Sandgussverfahren verarbeitet werden kann, stellt einen zusätzlichen Vorteil dar. Neben gängigen Metallen wie Stahl, Aluminium und Gusseisen lassen sich auch Legierungen mit spezifischen Eigenschaften problemlos einsetzen. Diese Anpassungsfähigkeit an unterschiedliche Werkstoffe eröffnet vielseitige Anwendungsmöglichkeiten in verschiedenen Industrien, von der Luftfahrt über den Maschinenbau bis hin zur Energietechnik. Durch die Kombination von Flexibilität, Wirtschaftlichkeit und Materialvielfalt ist das Sandgussverfahren ein unverzichtbares Werkzeug in der modernen Fertigung und trägt dazu bei, innovative und funktionale Lösungen für eine Vielzahl technischer Anforderungen zu schaffen.
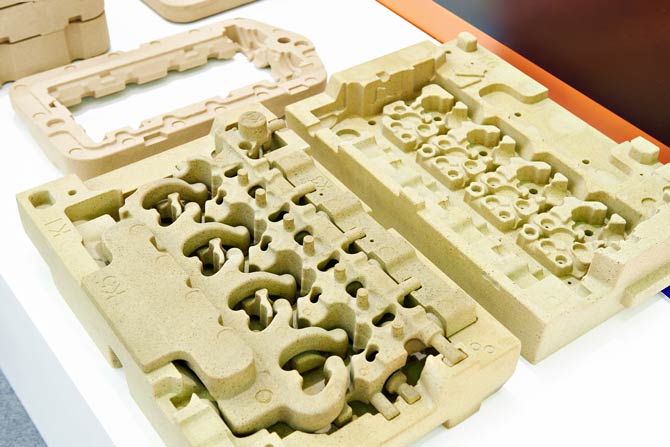
Anwendungen und Bedeutung in der Industrie
Das Sandgussverfahren ist aufgrund seiner Vielseitigkeit ein fester Bestandteil zahlreicher Industriezweige. In der Automobilindustrie wird es vor allem für die Herstellung von Motorblöcken, Zylinderköpfen und Getriebegehäusen genutzt. Diese Bauteile erfordern eine hohe Präzision und Belastbarkeit, die durch die Eigenschaften des Sandgusses erreicht werden können. Im Maschinenbau kommen häufig größere und komplexe Komponenten wie Pumpengehäuse, Turbinengehäuse oder Grundgestelle zum Einsatz, die ebenfalls vom Sandgussverfahren profitieren. Auch in der Luftfahrtindustrie wird der Sandguss genutzt, etwa für die Fertigung von Triebwerkskomponenten oder strukturellen Bauteilen, bei denen Gewicht und Stabilität entscheidend sind.
Neben der Serienproduktion spielt das Sandgussverfahren eine wichtige Rolle bei der Herstellung von Prototypen. Es können durch die vergleichsweise geringe Vorlaufzeit und die kostengünstige Formherstellung Konstruktionen schnell umgesetzt und getestet werden. Dies ist insbesondere in der Produktentwicklung von Vorteil, um innovative Designs effizient zu validieren.
Auch bei der Fertigung von Ersatzteilen hat der Sandguss einen hohen Stellenwert.
Vor allem bei seltenen oder nicht mehr lieferbaren Bauteilen kann das Verfahren eine wirtschaftliche Lösung bieten. Einzelstücke oder Kleinserien werden präzise und anwendungsspezifisch gefertigt, ohne dass teure Dauerformen erforderlich sind. Die Bedeutung des Sandgusses in der Industrie ergibt sich aus seiner Fähigkeit, komplexe Geometrien, vielseitige Materialien und flexible Produktionslösungen zu vereinen. Dies macht das Verfahren unverzichtbar für eine Vielzahl technischer und wirtschaftlicher Anwendungen.
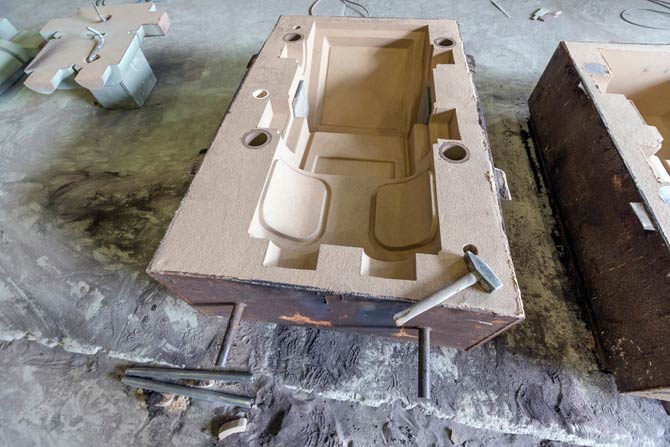
Einschränkungen und Herausforderungen
Trotz seiner Vielseitigkeit weist das Sandgussverfahren einige Einschränkungen auf, die je nach Anwendungsbereich berücksichtigt werden müssen. Im Vergleich zu anderen Gießverfahren, wie beispielsweise dem Feinguss, ist die Genauigkeit bei Maßtoleranzen sowie die erreichbare Oberflächenqualität begrenzt. Dies liegt an der Struktur des Formsandes, die nicht die glatte Oberfläche und präzisen Konturen ermöglicht, die durch andere Verfahren realisiert werden können. Daher sind bei bestimmten Anwendungen zusätzliche Nachbearbeitungsschritte erforderlich, um die gewünschte Oberflächenbeschaffenheit zu erreichen.
Ein weiterer Aspekt ist die Abhängigkeit des Verfahrens von den Eigenschaften des verwendeten Formmaterials. Die Wahl und Qualität des Formsandes sowie der Bindemittel beeinflussen direkt die Stabilität der Form und damit die Qualität des Gussstücks. Schwankungen in der Materialzusammensetzung oder unzureichend angepasste Sandmischungen können zu Fehlern wie Rissen oder Verformungen führen. Diese Abhängigkeit erfordert eine sorgfältige Materialauswahl und Kontrolle während des gesamten Prozesses.
Die Verwendung von Formsand bringt auch Herausforderungen im Hinblick auf Umweltaspekte mit sich.
Der Sand wird nach dem Guss häufig entsorgt, da er durch den Prozess thermisch und chemisch belastet wird. Obwohl Recyclingtechniken existieren, um gebrauchten Sand wiederaufzubereiten, sind diese Verfahren oft aufwendig und mit Kosten verbunden. Gleichzeitig gibt es Bestrebungen, umweltfreundlichere Materialien und Bindemittel einzusetzen, die eine nachhaltigere Nutzung ermöglichen könnten.
Zukunft des Sandgussverfahrens
Das Sandgussverfahren steht vor einem Wandel, der durch technologische Innovationen und moderne Entwicklungen geprägt wird. Neue Materialien und Verfahren zur Verbesserung der Formstabilität und Gussqualität tragen dazu bei, die Grenzen des bisherigen Prozesses zu erweitern. Fortschritte in der Werkstoffforschung ermöglichen die Verwendung hochspezialisierter Sandsorten und Bindemittel, die auf spezifische Anforderungen zugeschnitten sind. Gleichzeitig wird der Einsatz additiver Fertigungstechniken, wie der 3D-Druck von Sandformen, zunehmend zu einer Schlüsseltechnologie. Diese Innovationen bieten eine höhere Flexibilität und eröffnen neue Möglichkeiten für komplexe Geometrien.
Nachhaltigkeit spielt eine immer größere Rolle bei der Weiterentwicklung des Sandgusses. Die Optimierung von Recyclingprozessen für gebrauchten Formsand und die Entwicklung umweltfreundlicherer Bindemittel sind zentrale Ansätze, um den ökologischen Fußabdruck zu reduzieren. Gleichzeitig wird an energiesparenden Gießverfahren und der Nutzung erneuerbarer Energien gearbeitet, um den Gesamtprozess nachhaltiger zu gestalten.
Die Automatisierung und Digitalisierung des Sandgussverfahrens verändern die Fertigung grundlegend. Intelligente Steuerungssysteme, Sensorik und Datenanalyse verbessern die Prozessstabilität und ermöglichen eine präzisere Kontrolle der einzelnen Arbeitsschritte. Der Einsatz von Robotik in der Formherstellung und Nachbearbeitung steigert die Effizienz und reduziert menschliche Fehler. Zudem fördern digitale Zwillinge und simulationsbasierte Ansätze die Planung und Optimierung des gesamten Produktionsprozesses.
Diese Entwicklungen zeigen, dass das Sandgussverfahren auch in Zukunft eine wichtige Rolle in der Fertigungstechnik spielen wird. Durch die Kombination von Innovation, Nachhaltigkeit und Automatisierung wird das Verfahren kontinuierlich an neue Anforderungen angepasst.